Production & Quality Control
- Services
- Production & Quality Control
Key Activities
Do You Need?
Increase brand visibility
Follow Us
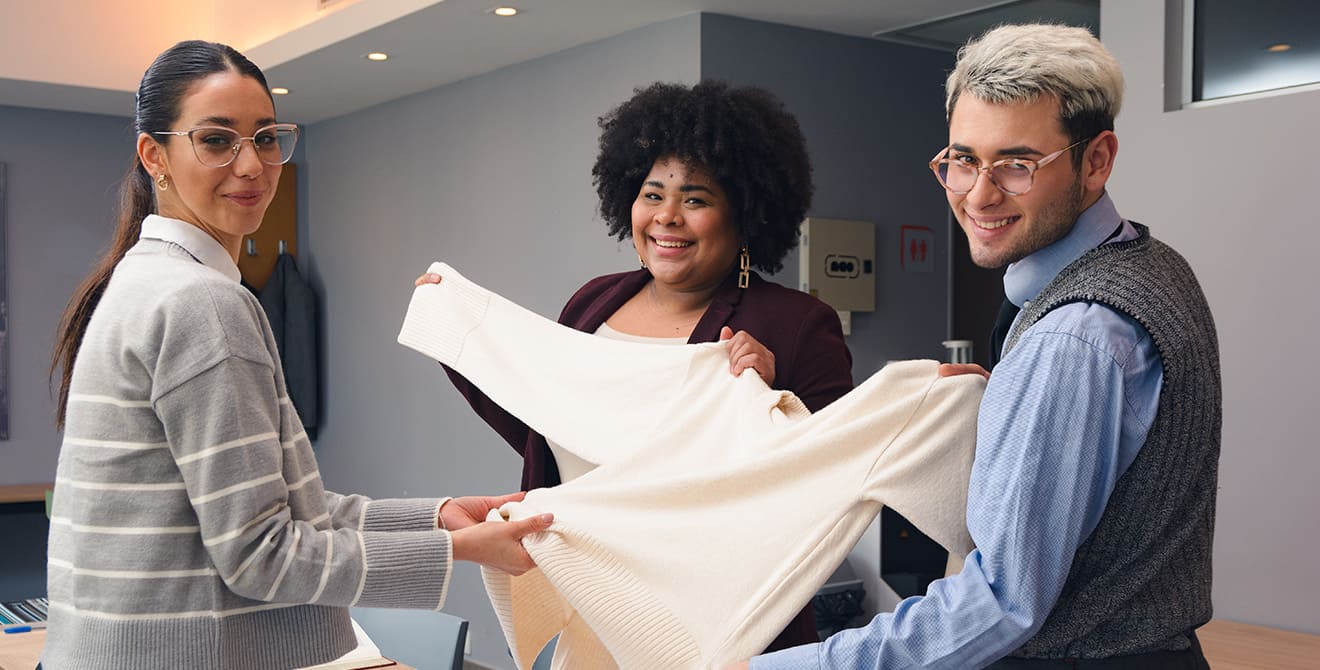
Marketing & Merchandising
Production is the end-to-end process of converting raw materials, ideas, or data into finished goods or services that meet customer requirements—on time and at cost.
Core Activities
- Planning & Scheduling: Forecasting demand, creating master production schedules, balancing capacity vs. workload.
- Procurement & Materials Management: Sourcing raw materials, ensuring just-in-time deliveries, and maintaining optimal inventory levels.
- Process Engineering: Designing efficient workflows, line balancing, and selecting machinery / automation.
- Manufacturing Execution: Operating equipment, monitoring output, and coordinating labor to hit daily targets.
- Maintenance: Preventive and predictive upkeep to minimize downtime and extend asset life.
- Cost Control: Tracking direct and indirect costs, implementing lean/Kaizen, and driving overall equipment effectiveness (OEE).
Quality Control is the systematic set of procedures and inspections used to ensure that products meet defined standards and customer expectations before release.
Core Activities
- Incoming Inspection: Verifying raw materials and components against specifications.
- In-Process Checks: Sampling and testing during production to catch defects early.
- Final Inspection & Testing: 100 % or statistical sampling of finished goods for dimensional, functional, and aesthetic compliance.
- Documentation & Traceability: Maintaining test records, lot numbers, and certificates of analysis for transparency and audits.
- Corrective & Preventive Actions (CAPA): Root-cause analysis of defects and implementation of preventive measures.
- Compliance & Audits: Adhering to ISO, ASTM, or customer-specific standards and passing internal/external audits.